by Chelsea Williams | Jan 8, 2018 | Uncategorized
The New Year is here! Are technology changes on your calendar?
Visibility is perhaps the most business-critical issue in manufacturing and warehousing today. You need easily accessible, real-time data across your supply chain. With the growth of warehouses (both in number and size), the soaring number of SKUs you’re juggling, and the squeeze on your profit margins, you can’t allow any weak links to exist in your supply chain.
At Informs, we’re looking ahead at the view of visibility in 2018 and the manufacturing technology trends—and how our customers can benefit from making change. It’s not just about the rapid ROI you gain but repairing the profit leaks from outdated systems and technology.
Here’s what we’re seeing for the year ahead.
-
-
- An even greater increase in the deployment of advanced mobile technology. Rugged mobile devices—handheld computers, tablets, scanners, imagers, thermal printers—will replace consumer-grade devices. Employers are discovering that the cost of replacing personal smartphones and tablets that last less than a year is too high. Plus, they need enterprise-grade features—like better data and network security, device management, and data capture—that only purpose-built, commercial grade technology can deliver.
-
- Real-time tracking is not optional. A Zebra study reported that 63% of manufacturers surveyed are planning to upgrade to technology-driven tracking in the next five years, to improve real-time visibility; 60% of warehouses responded that they are moving to real-time location tracking by 2022, a 25% jump from 2017.
-
- Wearables are in fashion. Every motion contributes to the bottom line cost. Equipping pickers, for example, with wearable computing technology (wrist terminal, ring scanner, computer headset) is proven to deliver ROI. A VDC Research study showed 85% of warehouses surveyed are planning to integrate wearables to increase employee productivity.
-
- Multi-modal is also a hot topic. Voice-directed picking (VDP) provide an advantage over manual picking, but multi-modal speech-directed solutions provide even greater results. VDP users require the direction to be repeated 381% more often and have an error rate that’s 63% higher than multi-modal system users.
-
- RFID and IoT deliver substantial ROI. The connected factory works more efficiently, with better communication, fewer delays and errors, and reduced downtime. Using both technologies enables lean manufacturing processes. Smart sensors alert operators to potential problems, like equipment failures and replenishment needs, so that they can be proactively managed. RFID enables workers to manage inventory from inbound to outbound. With RFID-enabled vehicle-mounted computers, forklift operators can work continuously, without stopping, starting, and getting in and out of the vehicle.
This continued shift toward maximizing efficiency and accuracy is not a trend as much as it is an initiative. Technology continues to evolve to empower manufacturers and warehouse operations to work smarter. Informs is staying ahead of these changes, and we can help you navigate your business technology to capitalize on the many benefits. Contact us to talk about your current situation and your vision of 2018.
by Chelsea Williams | Dec 10, 2017 | Uncategorized
What can we expect for data collection trends in 2018? We compiled a list of the enterprise-level technologies we think will have the most impact on the supply chain.
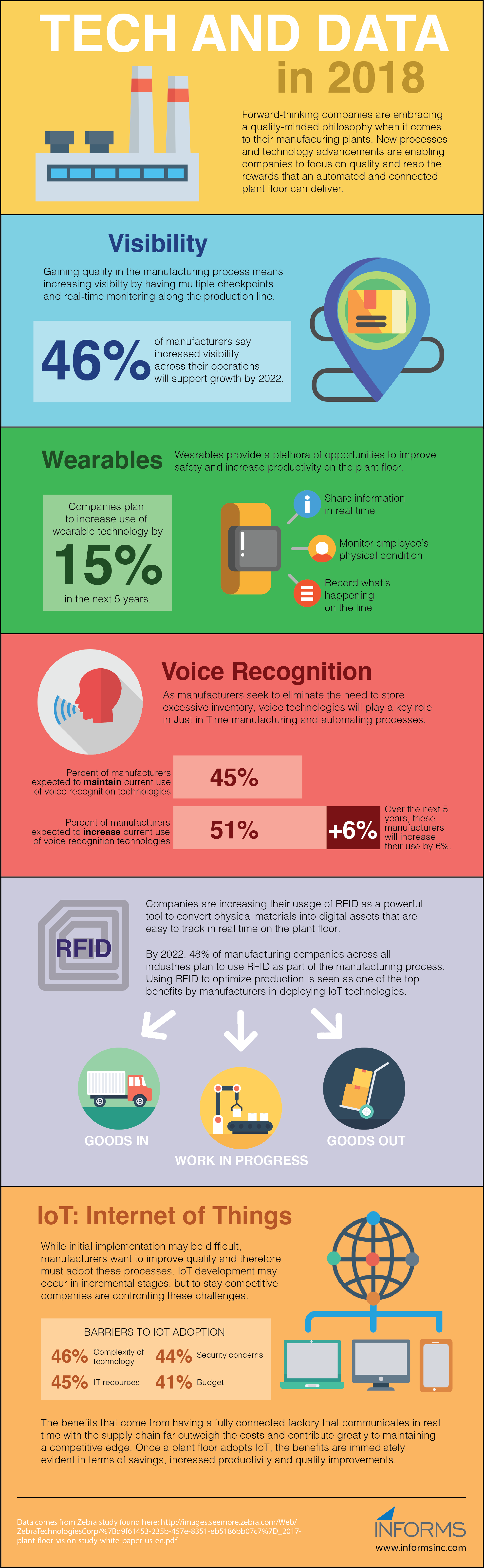
by Chelsea Williams | Nov 28, 2017 | Uncategorized
Operational productivity in the DC or warehouse depends on a number of factors, but when it comes to your cordless devices, like handheld scanners or mobile computers, success rests with the batteries they run on. To ensure long life and maximum up-time, here are 6 best practices for mobile device battery health.
- Label Each Device
As soon as you receive it, number and label each device critical to your mobile strategy. Labeling each unit helps to keep tabs on them – for example, you’ll always know if a bar code scanning device is charging, or if a device is missing at the end of a shift. As you insert replacement batteries for your handheld devices, you can rest assured you have a freshly charged battery and spares, if needed.
- Label Charger Slots and Batteries
By assigning batteries and charging slots to specific devices, you can tell at a glance if one is missing. With a spare battery charging for each device, workers can easily swap their depleted batteries without risking extended downtime.
- Replace Batteries at the Right Time
Every battery has an expected lifespan, and while the battery may still operate beyond the expected timeframe, you will experience reduced efficiency. The battery will no longer charge as fully as it once did, so workers may have to change batteries in the middle of a shift, or they may have to scan items multiple times before the device can read the bar code. Most batteries in daily rotation should be replaced every 12 to 18 months, depending on the number of shifts in operation.
- Mark Batteries with the Purchase Date
Knowing how long your mobile computer batteries have been in rotation will help you plan the optimum replacement cycle, making it easier for you to ensure you have enough fresh batteries for every device. Some people write purchase dates on the device while others use colored stickers to denote the month and year of purchase. Keeping track of the colors assigned to each month is a little extra work up front, but it makes it easier to visually scan your battery supply to see how many are due for replacement. Whichever method you choose, tracking service cycles help ensure you won’t lose productivity because of weak batteries.
- Invest in Spares
You should always have at least one and preferably two spare batteries per device. This helps ensure you always have a fully-charged battery available and eliminates unnecessary downtime because of battery availability. Don’t forget to label the spares the same way you do the main batteries.
- Perform Regular Battery Maintenance
Dirt and debris are the enemy of well-charged batteries. Periodically clean the contact terminals with a soft lint-free cloth to keep the battery clean and charging freely.
Consider Battery-Free Devices
The latest scanning devices, such as the Honeywell Voyager 1200g-bf, use supercapacitors rather than batteries for power. These devices hold their charge for about 100 scans, but recharge in just a few seconds. They are ideal for retail scanning or any scanning application where the device is not in continuous use for extended periods. You can learn more about this technology here.
by Chelsea Williams | Nov 20, 2017 | Uncategorized
T
he holiday season has begun. To stay ahead of customer demands and outwit the competition, efficient fulfillment is the key to your success. Have you taken these steps to ensure your DC is ready?
- Training
If you are bringing on temporary team members to manage the extra workload, you need them to become productive quickly. However, you don’t want to invest a lot in training since these new workers will be gone after the holidays. If you have a continuous improvement program in place, you may have already made a good start to simplify your processes, which will make it easier to bring new people on board. This is not the right time to make sweeping changes to procedures, but small tweaks may help you keep productivity high.
You should also invest in mobile devices that are simple and intuitive to use, and make sure they know how to operate the devices. Show new employees how to scan bar codes using a handheld scanner or mobile computer, and how to change the batteries or recharge cordless devices. Don’t forget about loading labels! Temporary employees need to know
how to replenish bar code label printers, and where to go if they run in to a problem they can’t solve on their own.
Giving your temporary employees a thorough grounding in your equipment and procedures will help them to become productive faster and keep them from becoming a drain on the productivity of your experienced staff.
- Workforce Preparation
Make sure you have enough devices, spare batteries, chargers and accessories to supply each worker, and make sure they have a keen understand of the business processes they need to perform. Equipping users with the right data collection devices will not only keep productivity high but may also improve safety by reducing accidents. For example, arming your workers with hands-free bar code scanners or a voice-directed data collection solution will speed up productivity, allowing them to spend more time on the task and less time fiddling with the device.
- Select Devices for Efficiency and Reliability
Your entire team needs to move fast during the holiday season and other peak times of the year, so be sure your devices are up to the task. If your mobile devices are not rated for the rigors of a rugged distribution center or warehouse, or if your handheld scanners are not as responsive as they need to be for your fast-paced environment, it can lead to a decrease in order accuracy, increased rates of failure and additional expenses to correct mistakes. Printer volumes may also become an issue if you are asking your printer to exceed its rated duty cycle.
The Right Device Makes All the Difference
Choose rugged devices that can stand up to untrained and multiple users, drops to concrete and changes in environmental conditions. Consider the ergonomics of the device. You may want wireless scanners for the shipping area and forklift mounted devices or mobile terminals for the picking team. In the long run, it will save you time and money to choose devices wisely rather than focus on pricing. The right mobile devices can reduce costs and errors while increasing productivity and customer satisfaction.
Your employees will be picking, packing and shipping at break-neck speed, so having the right equipment will help keep them safe and improve accuracy while minimizing potential damage to your devices. The bottom line is that in a short amount of time, you’ll need to be on top of your game with speed and accuracy to satisfy customer requirements.
by Chelsea Williams | Sep 26, 2017 | Uncategorized
In today’s competitive environment, a company’s success rests squarely on the effectiveness of its supply chain. An effective supply chain requires fast transactions and accurate inventory, making a complete professional-grade labeling solution a must‑have. A complete professional labeling solution means the company has hardware that suits its environment, the right type of labels it needs, and software that makes printing the right labels effortless.
You might ask, “why is the labeling solution such a critical component?” The answer is simple. In order to be successful today, you simply must have
an extremely efficient operation. From a competitive standpoint, it’s critical; if your competitor can get product out the door fast and efficiently, then you need to be doing the same. If you’re not using barcode automation in the warehouse, distribution center or manufacturing floor, you’re already a few steps behind. To take that first step, find a solution provider who understands your business and has proven success in your industry. The next step is to educate yourself on the benefits of implementing a labeling solution like a pro:
- Simplified Compliance. A professional labeling solution makes label changes easier and helps ensure compliance. Centralized management portals and remote maintenance make it easy to update label formats or add newly required information. This helps the company avoid costly recalls and expensive fines. Don’t risk losing business due to non-compliant labeling.
- Greater Supply Chain Efficiency. Accurate and fast transaction processing are keys to supply chain efficiency, and clearly-printed barcode labels are the cornerstone of any transaction processing system. Using barcode labels increases accuracy by preventing data entry mistakes, incorrect picking or shipping mishaps. Barcode scanning is a much faster and accurate alternative to manual processes, so worker productivity benefits from an automated process as well.
- Branding Standards. A professional labeling solution has a better chance of producing clearly-printed, correctly issued labels; companies often rely on pre-printed labels, which can be quite costly and unreliable in terms of supply. You want your labeling to properly reflect your brand – which means you want the label to look the same every time it’s printed. This includes your logo, certifications, trademarks, patents and critical information about the item being labeled. This ensures consistency from unit to unit and makes in-house transactions faster. It also helps supply chain partners become more productive since they know what to expect from your label. Professional-grade labels also help make counterfeiting harder and more visible if it occurs, so it is easier to identify and stop.
- Business Continuity and Risk Mitigation. A professional-grade labeling solution allows you to shift production from one location to another without excessive downtime or reconfiguration. Label templates can be loaded remotely to printers in other locations in the plant or even in another plant altogether, ensuring that production and shipments continue and that product continues to be labeled properly regardless of any interruptions.
- Better Flexibility and Responsiveness. Professional labeling solutions offer multi-language capabilities and simple label changes that workers can make easily—even on the fly. This allows you to offer customized labels to customers in other regions or to customers with unique branding requirements of their own.
- Enhanced Collaboration and Communication. Your entire supply chain depends on the accuracy of your labeling, so centralized label control and professional grade printed labels help to ensure supply chain efficiency and accuracy as your goods move from node to node. This prevents rework or shipping errors that may occur due to labeling errors, and it reduces the risk of counterfeit goods entering the supply chain. As a result, your company enjoys lower costs and higher potential revenues.
You don’t have to invest a lot in order to gain the operating efficiency and productivity benefits of a complete labeling system. If you’re spending a lot of time and money on labeling logistics in your business, consider speaking with a solution provider who is an expert in the industry. Not sure who to contact? Try us! We can give you plenty of examples of the improvements businesses have made by making the switch to a solution that best suits their needs.
by Chelsea Williams | Sep 19, 2017 | Uncategorized
As companies release new products or make enhancements to existing products, they often retire the old versions and the legacy product goes ‘end-of-life’ (EOL). Just because a company releases an updated version of something you already own doesn’t mean the existing product has no utility. It does mean it’s time to start thinking about what the newer technology offers and whether it makes sense for your business to upgrade.
Getting the Most from Your Old Products
Before deciding whether to upgrade or stay with your existing version, talk to your reseller to understand the benefits the newer version provides. Don’t forget to factor in the possibility of trading in your old device, and ask about any ongoing promotions or incentives being offered if you purchase the next gen product. Then be sure to conduct a cost justification analysis, to validate the expense of purchasing replacement product before making a final decision.
If you have a year of support services prepaid on your existing model, determine the best time to make your move. If it’s a technology product that’s more than five years old, the newer device will likely offer greater operating efficiency. You’ll also want to compare specifications (speed, reliability and new features) which may easily outweigh any cost advantage of keeping an old device in service.
Create a Plan
You should always have a replacement and service strategy plan in place for critical devices. This can help ensure you are getting the best ROI for your device investment without introducing undue risks of downtime or service interruptions. It can also help prevent wasting money on the “next big thing” while you still have useful life in your existing devices. Here are three steps to create a good technology replacement strategy.
- Plan
Always have a replacement plan for technology refreshes for critical devices. Don’t wait until products go EOL to decide. Understand the typical life cycle of your devices, and balance the costs of maintaining existing devices with the replacement costs so you know the right replacement cycle for your needs. The earlier in a product’s life cycle you make this plan, the easier it will be to time the replacement for optimum ROI and utility and to ensure you have budget available when needed. Be sure to connect all the dots in your solution in order to properly budget expenses of any equipment purchases you’ll need to make.
- Protect
For your most critical devices, you may want to consider a service contract. The more complex the device, the more important it is to have service coverage. For mobile computers, a service contract helps protect your investment and your overall budget by ensuring that repair and maintenance costs are predictable. Most service contracts also include preventive maintenance, so this option can help extend the useful life of your devices while protecting your cash flow from unexpected demands.
- Extend
If your existing products are operating efficiently, you may want to extend any existing service contracts rather than introduce new products to your facility. Extending contracts ensures you receive all the utility you paid for when you bought your devices and can maximize return on investment (ROI). A service contract keeps the unit in good working condition, particularly contracts that include software updates, which may extend the average life of the device.
A Real Life Example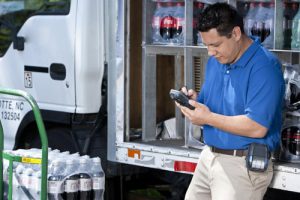
Honeywell has announced that its CK71 handheld computer will be entering the end of life stage on December 30, 2017. The CK75 is the replacement model. Some factors to consider:
- Honeywell has announced that it will continue to provide service for the CK71 for some time into the future. Keep these dates in mind to ensure your new plan is in place before then.
- The CK75 is smaller, lighter and more rugged than its predecessor, so it will help your team be more efficient.
- The CK75 also runs both Windows® Embedded and Android™, so it offers protection from OS life cycles.
- The barcode scanner on the CK75 offers superior accuracy and speed, so your team can operate more efficiently with fewer errors or rescans.
What’s Next?
The decision to replace an end-of-life product is not easy. It helps to consult with an experienced reseller who understands the products, your application, and the advantages a next generation product can offer. If you’re looking for a recommendation or just looking for a market update on the technology being used to maximize productivity in your industry, contact us today.
Recent Comments